
The first image below shows a blade with a moderate rake angle. A tooth with a 0° rake angle will have it's face aligned perfectly with a line drawn through the center of the blade. Blades used for cutting non-ferrous metals and plastics typically have a 0° rake angle. The beveled tooth is beveled on both sides and flat on top.Īnother characteristic is the rake angle. The teeth alternate from straight to beveled. The teeth are in a TCG (Triple Chip Grind) configuration. The second blade is a more specialized blade. This is an ATB (Alternate Tooth Bevel) blade. The teeth on the following blade are in the most common configuration. These are much more durable and can last for many years if not abused.īlades come in different configurations. The better blades have carbide teeth welded or brazed onto the steel. These are budget blades and are rarely used. You'll see standard blades with teeth simply cut from the material that makes up the rest of the blade. To understand some of the following information, you'll need to know a bit more about circular saw blades. Since my experience is mainly with thin acrylic sheeting (1/2" or less), that's what I'll cover. There are a couple of different ways to cut acrylic. If the edge has to be straight and square, a table saw with the right blade is what you'll need to use to make the cuts (especially in materials thicker than 1/8"). If the cut/finished edge will be against another piece of straight material when it's installed, a slight dip in the edge (which can be caused by hand finishing) can look very bad. Sanding, filing and scraping go very slowly, especially on rough surfaces. It's VERY time consuming to have to fix the results of a bad cut. It may seem that you could easily fix any roughness in the edge with a bit of sandpaper. When cutting acrylic for applications where the edge will be visible and will need to be either polished or at least very smooth, it's absolutely imperative that you get the cut right the first time. Unlike glass, glass cleaners (like those with ammonia) can damage some acrylic. When cleaning the acrylic material, only use cleaners that are approved by the manufacturer.
Flexiglass final free#
If the application requires that the surface is scratch free (for a show vehicle, etc.) leave it on until it's about to be installed in the vehicle. The material can be scratched relatively easily. From this point on, I'll refer to it simply as acrylic.ĭo not remove the film or paper protector from the acrylic until you absolutely have to.
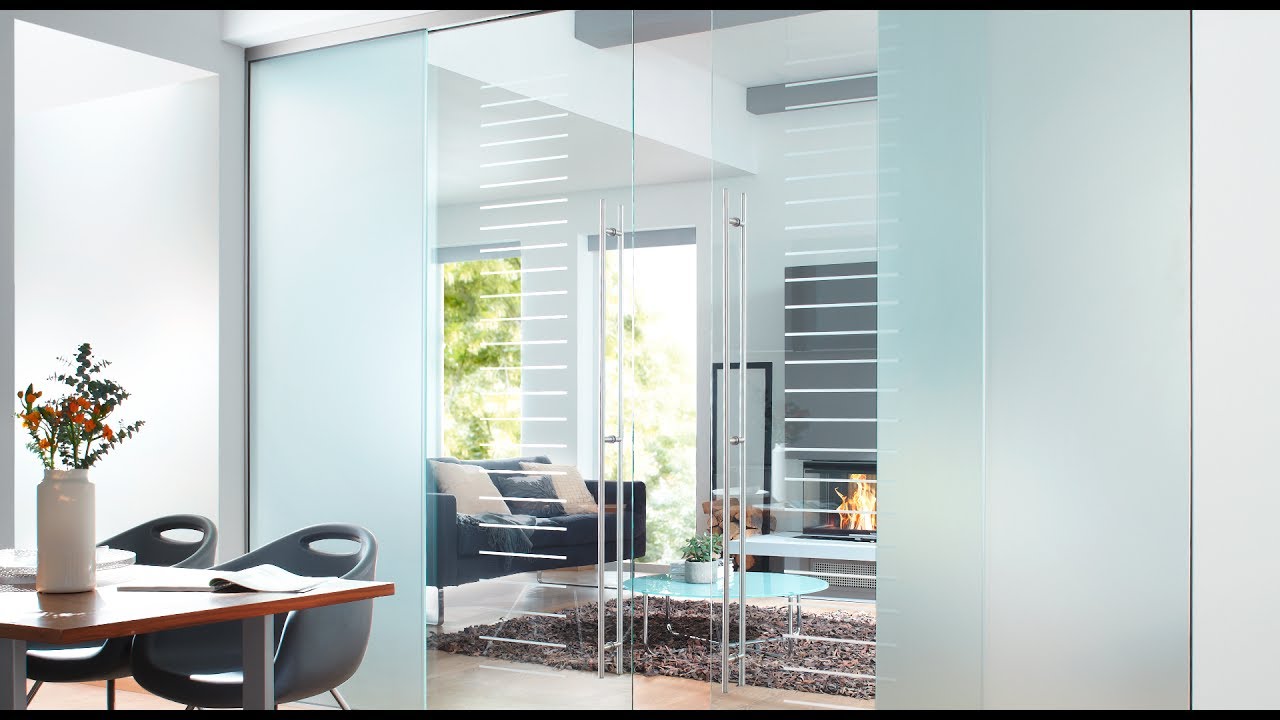
The same acrylic type sheeting is also known by the names Acrylite ©, Lucite © and Perspex ©.
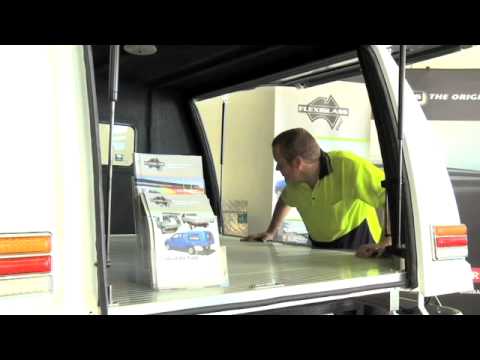
Plexiglass ©, however, is the name given to acrylic sheeting manufactured by Atofina.
Flexiglass final software#
It's not quite as simple as Ruffle but anyone even moderately familiar with the Windows Control Panel and installation of software can use Flash as it was intended.Īcrylic sheeting is widely known as Plexiglas ©. More information on Flash capable browsers can be found HERE.
Flexiglass final portable#
An alternative to Ruffle for viewing Flash content is to use an alternative browser like the older, portable version of Chrome (chromium), an older version of Safari for Windows or one of several other browsers.
